Casting Aluminum Illinois: Your Comprehensive How-To Handbook
Casting Aluminum Illinois: Your Comprehensive How-To Handbook
Blog Article
Precision and Excellence: Best Practices for Successful Aluminum Spreading
In the world of light weight aluminum spreading, achieving precision and perfection is not merely a goal however a criterion that differentiates quality. The precise process of aluminum casting demands attention to detail at every phase, from product option to last finishing touches.
Material Option
When taking into consideration material selection for light weight aluminum casting procedures, resilience, and warm resistance are vital factors to review,. Aluminum alloys supply a variety of choices, each with special buildings that can significantly influence the high quality and performance of the final casted product. One usual selection is the 356 alloy, understood for its exceptional fluidity and resistance to deterioration, making it appropriate for a range of applications. For high-stress atmospheres requiring exceptional stamina, the 7075 alloy stands apart as a result of its high strength-to-weight ratio. Furthermore, the 6061 alloy is favored for its great weldability and formability, making it a versatile option for elaborate styles.
In the choice procedure, it is vital to take into consideration not just the mechanical properties of the alloy but likewise its thermal qualities. Warm resistance is necessary to ensure that the casted part can endure the temperature levels it will be exposed to throughout procedure without endangering its structural integrity. By carefully evaluating the durability and warm resistance of different aluminum alloys, producers can make informed choices that result in premium, dependable casted products.
Mold And Mildew Layout
In the realm of aluminum casting finest techniques, an integral aspect that dramatically influences the final product's top quality and integrity is the thorough design of the mold and mildew. Mold and mildew layout plays a crucial duty in identifying the dimensional accuracy, surface finish, and general ins and out of the actors aluminum part. When producing a mold for aluminum spreading, several vital elements should be taken into consideration to guarantee optimum outcomes.
First of all, the mold design ought to account for the product flow attributes of molten aluminum to avoid problems such as shrinking, porosity, or misruns. Appropriate gating and riser placement are important elements in the mold and mildew design process to promote smooth metal circulation and decrease the formation of air pockets.
Additionally, the mold layout ought to take into factor to consider the cooling price of the aluminum to stop breaking or distortion during solidification. Adequate venting and cooling down channels within the mold and mildew can assist regulate the temperature level distribution and promote consistent solidification of the steel.
Refine Optimization
To improve performance and high quality in aluminum casting, procedure optimization plays a pivotal function in simplifying procedures and making the most of output. By fine-tuning each action of the casting process, suppliers can determine traffic jams, decrease waste, and enhance overall productivity.
Moreover, implementing lean manufacturing principles can additionally boost procedure optimization in light weight aluminum spreading. By eliminating non-value-added activities and focusing on continuous enhancement, makers can achieve greater effectiveness levels and much better source utilization. In addition, normal surveillance and analysis of essential performance indicators (KPIs) assist in identifying locations for improvement and making data-driven choices to enhance the spreading process consistently.
Top Quality Control
Refine optimization in aluminum casting not just boosts effectiveness and productivity but additionally lays the foundation for strict high quality control measures to promote sector standards. Quality assurance is paramount in ensuring that last aluminum castings satisfy the needed requirements and efficiency requirements. Executing an extensive quality assurance procedure involves different actions, beginning with the initial design stage through to the final assessment of the actors parts.
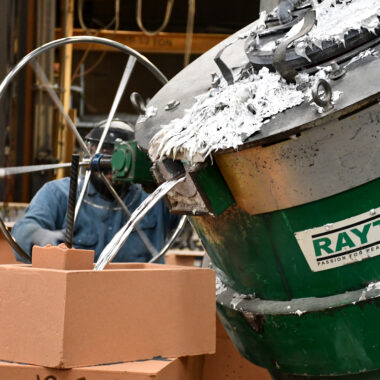
In addition, you can find out more developing clear quality control procedures and documentation treatments is necessary for monitoring and monitoring the spreading process. By maintaining detailed documents of manufacturing specifications, screening outcomes, and assessment reports, manufacturers can ensure consistency and traceability in their aluminum casting operations. Following rigorous quality control practices not only improves the general reliability of aluminum castings however likewise imparts confidence in customers regarding the top quality of the end products.
Finishing Techniques
How can light weight aluminum spreading be boosted via meticulous application of ending up strategies? Ending up techniques play an essential role in elevating the quality and aesthetic appeals of light weight aluminum spreadings. Among the main methods employed is surface smoothing, which involves the elimination of any type of flaws or harsh sides to browse around this site achieve a flawless finish. This process not just enhances the visual appeal of the casting yet also boosts its total functionality by making sure uniformity and precision.

Furthermore, methods like powder layer or painting can be put on light weight aluminum castings to supply both visual appeal and extra defense against environmental variables. By meticulously selecting and using the appropriate ending up techniques, makers can guarantee that their aluminum spreadings meet the highest criteria of high quality and performance.
Verdict
In conclusion, successful aluminum spreading requires precision and perfection in material selection, mold layout, procedure optimization, top quality control, and completing strategies. By adhering to ideal techniques in each of these areas, makers can make sure premium and regular cause their aluminum casting processes. casting aluminum illinois. It is necessary to see take notice of every detail and continuously aim for enhancement to attain optimal end results in aluminum spreading
The thorough process of light weight aluminum spreading demands focus to detail at every phase, from material option to final finishing touches.To enhance performance and high quality in aluminum spreading, procedure optimization plays a critical function in taking full advantage of and improving operations output.Refine optimization in light weight aluminum casting not only boosts effectiveness and productivity but additionally lays the structure for strict quality control actions to maintain industry requirements.One important aspect of top quality control in aluminum casting is the usage of advanced screening methods to assess the honesty and buildings of the castings.In verdict, effective light weight aluminum spreading requires accuracy and excellence in material choice, mold layout, procedure optimization, quality control, and ending up methods.
Report this page